Covid-19 is thought to originate from bats, and it is 96.2% similar to RaTG13 (collected by Shi Zhengli, Wuhan Institute of Virology, Chinese Academy of Sciences, in Yunnan, China in 2013) in nucleotide sequence level. However, it is a kind of novel coronavirus that has not been detected in humans and other animals before, and its appearance has brought many new problems to be solved urgently, including whether other pets, livestock and poultry may be infected by Covid-19 besides humans?
On April 8th, local time, the top academic journal Science published the paper "Susceptibility of Ferrets, Cats, Dogs, and Different Domestic Animals to SARS-coronavirus-2" online. The purpose of this study is to find out some questions: Will Covid-19 be transmitted to other animal species, thus becoming a "reservoir" of infection? Covid-19 infection has many clinical manifestations in humans, ranging from mild infection to death, so how is it manifested in other animals? With the development of vaccines and antiviral drugs, which animals can be used to simulate the effects of these drugs or vaccines on humans most accurately?
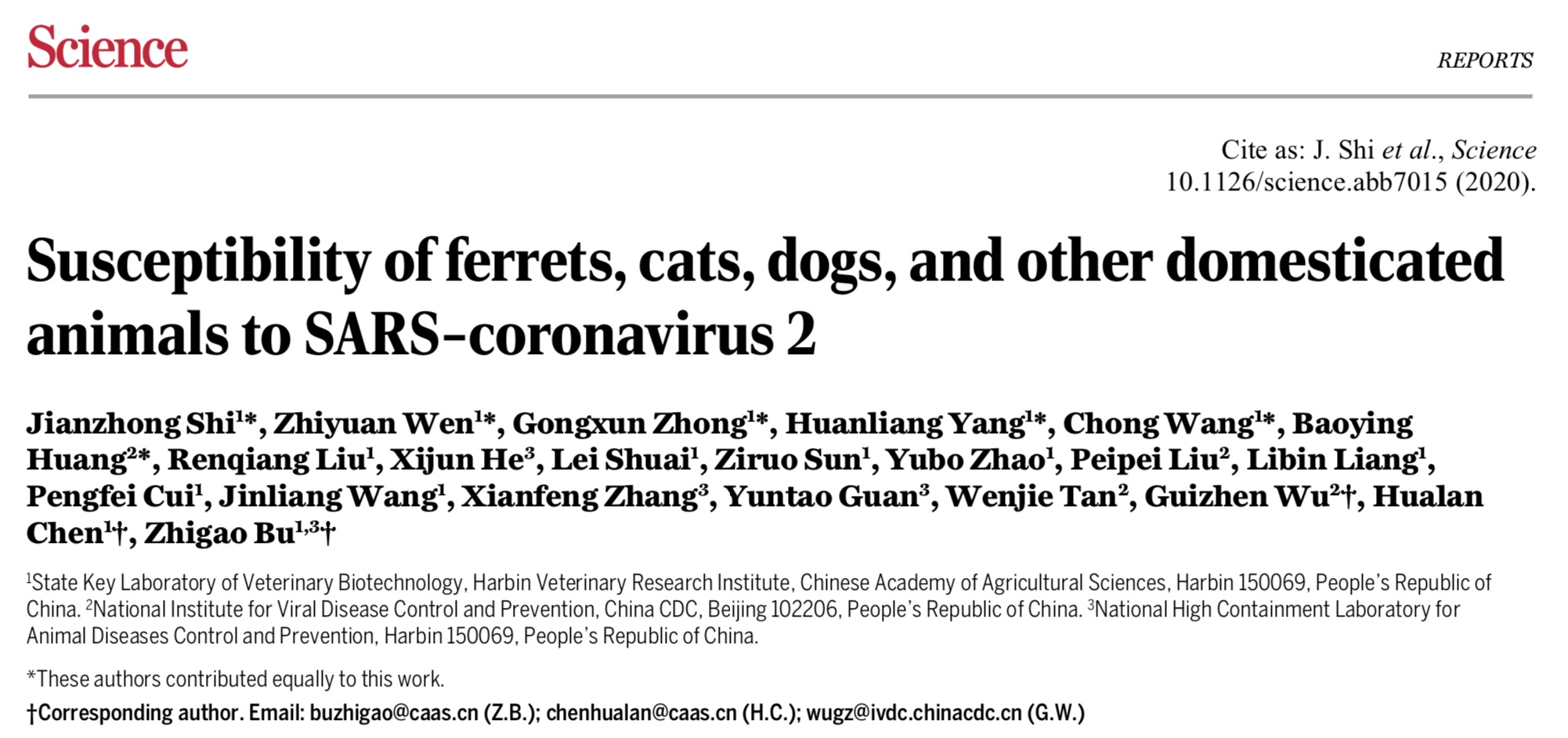
In order to solve these problems, research teams from the State Key Laboratory of Veterinary Biotechnology of Harbin Veterinary Research Institute of Chinese Academy of Agricultural Sciences and the National High-level Biosafety Laboratory of Animal Disease Prevention and Control evaluated the susceptibility of different model experimental animals, pets and livestock to Covid-19, infected Covid-19 through experiments, observed the clinical manifestations and pathological changes of vaccinated animals and cohabiting animals, and detected the viral load of organs and tissues, the emission of respiratory and intestinal viruses, and the seroconversion of antibodies against Covid-19 in animals.
Their research shows that Covid-19 has weak replication ability in dogs, pigs, chickens and ducks, but it can replicate efficiently in ferrets’ upper respiratory tract and cats’ respiratory system and digestive system. Experimental infected cats can spread Covid-19 through the air; Some cats can cause serious illness or even death after infection, and the illness of young cats is obviously more serious than that of older cats.
Histopathological observation confirmed that virus infection in cats can cause lung inflammation and intestinal mucosal damage to varying degrees. Immunohistochemical study showed that there were a large number of virus infections in mucosal epithelium and olfactory bulb cells of upper respiratory tract (nasal cavity, maxilla, tonsil), mucous gland epithelial cells of trachea and bronchial mucosa, and intestinal mucosal epithelium.
The correspondent of this paper is Chen Hualan, academician of China Academy of Sciences, chief scientist of the innovation team of animal influenza basic and prevention research in Harbin Veterinary Research Institute of China Academy of Agricultural Sciences, Bu Zhigao, director of Harbin Veterinary Research Institute of Chinese Academy of Agricultural Sciences and director of the national high-level biosafety laboratory for animal disease prevention and control, and Wu Guizhen, secretary of the Party Committee of Institute of Viral Disease Prevention and Control of China CDC and director of BSL-3 laboratory. Previously, on March 31st, local time, the research team had taken the lead in publishing the research on the preprint platform bioRxiv.
It is worth mentioning that the National High-level Biosafety Laboratory for Animal Disease Prevention and Control is one of the existing two P4 laboratories in China, and the other is in Wuhan National Biosafety Laboratory of Chinese Academy of Sciences. All the experiments of Covid-19 infection in this study were carried out in P4 laboratory, which was approved by the Ministry of Agriculture and Rural Affairs of China. Animal research and animal welfare programs were approved by the Animal Experimental Ethics Committee of China Academy of Agricultural Sciences.
According to the press release issued by official website, Harbin Veterinary Research Institute of Chinese Academy of Agricultural Sciences, different coronaviruses have been prevalent in mammals and poultry, but most of these coronaviruses are limited to specific species of animals and generally cannot infect humans. Similarly, several common coronaviruses in humans do not infect other animals. However, some coronaviruses from bats, such as SARS and MERS virus, can often infect many animals and humans.
At present, Covid-19 is popular among a wide range of people in the world, and the risk of introducing animals in close contact with human beings is increasing. Therefore, it is urgent to study the susceptibility of domestic animals in close contact with human beings to Covid-19, evaluate whether domestic animals are exposed to Covid-19 hazards and become potential intermediate hosts, and provide scientific basis for prevention and control of Covid-19.
In addition, in view of the current global epidemic situation of COVID-19, it is very likely that it will evolve into a common infectious disease, and it is urgent to establish a stable and reliable animal infection model to meet the needs of vaccine and drug research and development evaluation.
The research team stressed that the monitoring of cat COVID-19 should be regarded as an auxiliary means to eliminate the current Covid-19 epidemic. They called for close monitoring and protection of cats in epidemic areas, avoiding their contact with infectious sources and preventing them from becoming possible transmission hosts or storage hosts.
In addition, it was previously questioned that cats infected with COVID-19 were caused by large doses under laboratory conditions. However, in addition to this research, on April 3rd, Academician Jin Meilin, professor of the State Key Laboratory of Agricultural Microbiology of Huazhong Agricultural University, director of the Key Laboratory of Veterinary Diagnostic Preparations of the Ministry of Agriculture, director of the Research Center for Emerging Infectious Diseases of Wuhan Institute of Virology, Chinese Academy of Sciences, and researcher Shi Zhengli, director of the Key Laboratory of Highly Pathogenic Biology and Biosafety of Chinese Academy of Sciences, also published a study on the preprint platform bioRxiv. Through the investigation of cat serum, they found that the serum ELISA test of 102 cats collected after the outbreak of COVID-19 in Wuhan showed that the serum from 15 cats (14.7%) was positive for Covid-19 receptor binding domain (RBD).
Nadia, a 4-year-old tiger from Bronx Zoo in new york, USA, was recently diagnosed with Covid-19. On April 5, local time, the US Department of Agriculture issued a statement confirming that a tiger in a zoo in new york was diagnosed with Covid-19, and several other lions and tigers also showed symptoms of respiratory diseases. Officials at the Bronx Zoo in new york said that nadia, three other tigers and three African lions had symptoms of dry cough and loss of appetite, but they are expected to recover. Public health officials believe that these animals were infected by an asymptomatic employee.
Covid-19 can be replicated in the upper respiratory tract of ferrets for up to 8 days, but it will not cause serious illness or death.
Ferrets are often used as animal models of human respiratory viruses. Therefore, the research team first tested ferrets’ sensitivity to Covid-19.
Two Covid-19 strains were used in this study: F13-E from Wuhan South China Seafood Market and CTan-H from a patient infected with Covid-19.
The research team inoculated 10 5 PFU (Plaque Forming Unit) F13-E or CTan-H into ferrets through nose respectively, and euthanized them on the 4th day after inoculation (P.I.). The turbinate, soft palate, tonsil, trachea, lung, heart, spleen, kidney, pancreas, small intestine, brain and liver of each ferret were collected, and the viral RNA was determined by qPCR and virus titration.
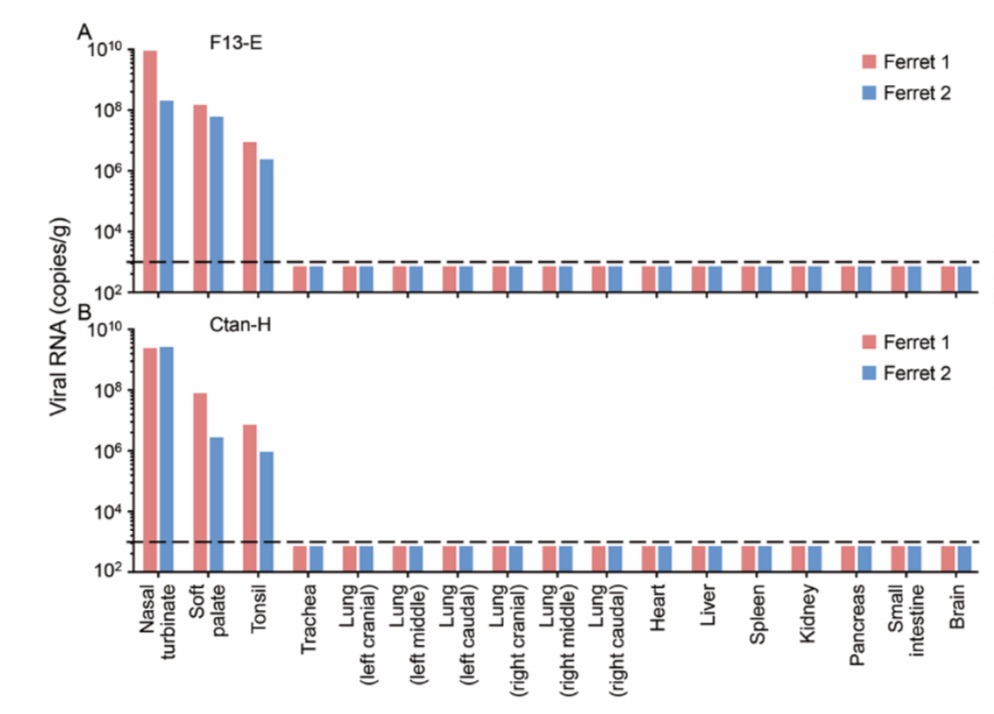
Viral RNA:A in ferrets’ organs or tissues: A, F13-E, B, CTAN-H..
The results showed that viral RNA and infectious virus were detected in the turbinate, soft palate and tonsil of all four ferrets, but not in other tissues.
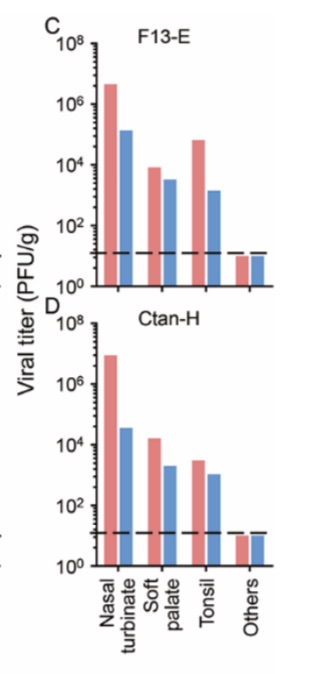
C, virus titer in organs or tissues of ferrets inoculated with F13-E, D and CTAN-H.
The research team believes that these results show that Covid-19 can replicate in the upper respiratory tract of ferrets, but it has not been detected in other tissues.
In order to study the replication dynamics of virus in ferrets, the research team intranasally inoculated 6 ferrets with 10^5pfu of F13-E(3) or CTan-H(3), and then placed them in three isolated cages. On the 2nd, 4th, 6th, 8th and 10th day, ferret nasal wash and rectal swab were collected for virus RNA detection and virus titration. At the same time, their body temperature and COVID-19 signs were monitored for two weeks.
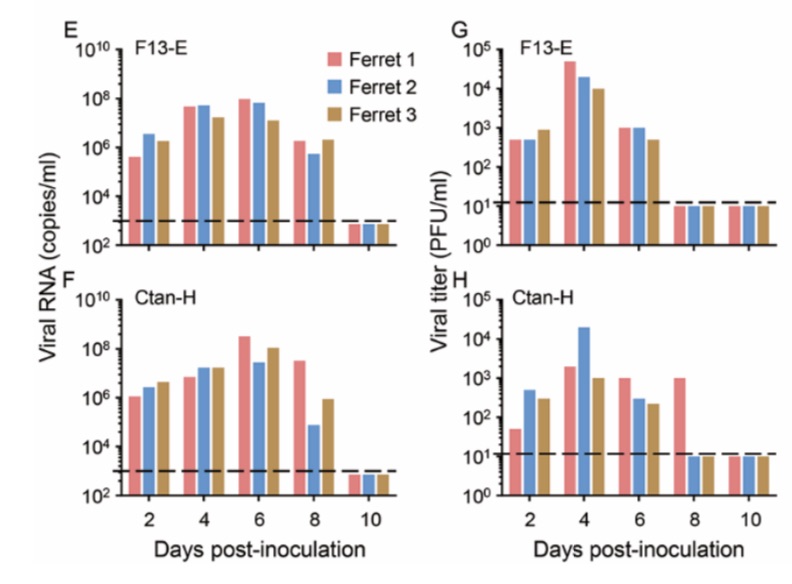
Viral RNA in the nasal wash of ferrets inoculated with F13-E(E) and CTan-H(F). Viral titers in the nasal wash of ferrets inoculated with F13-E(G) and CTan-H(H).
The results showed that viral RNA was found in the nasal wash of all six ferrets on the 2nd, 4th, 6th and 8th day. Viral RNA was also found in some rectal swabs, but the copy number was significantly lower than that of nasal wash. Infectious virus was detected in nasal wash of all ferrets, but none of them was found in rectal swab.
One ferret in each group developed fever and loss of appetite on the 10th and 12th days respectively. In order to investigate whether these symptoms are caused by virus replication in the lower respiratory tract, the research team euthanized the two ferrets on the 13th day and collected their organs for virus RNA detection.
However, except for the ferret turbinate inoculated with CTan-H, the low copy number was detected, and no viral RNA was detected in any other tissues or organs.
Pathological studies showed that two ferrets euthanized on the 13th day had severe lymphoplasmacytic vasculitis and vasculitis, the number of type II alveolar cells, macrophages and neutrophils in alveolar septa and alveolar cavities increased, and the lungs had mild bronchiolitis.
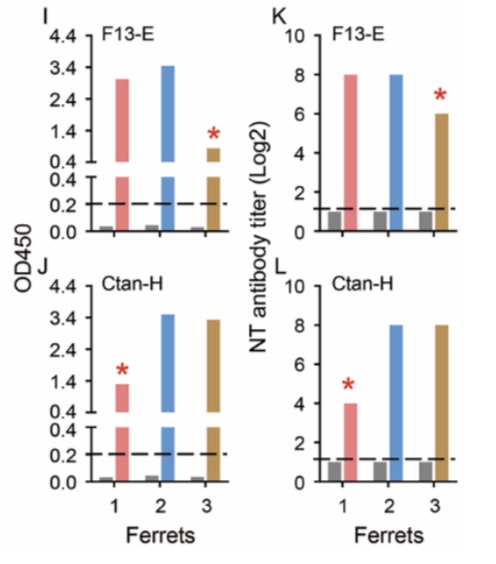
The asterisk indicates that the animals were euthanized on the 13th day after inoculation, and the other four animals were euthanized on the 20th day.
Covid-19 antibody was detected in all ferrets by ELISA and neutralization test, and the antibody titers of two ferrets euthanized on the 13th day were significantly lower than those euthanized on the 20th day.
In order to further study whether Covid-19 was replicated in ferrets’ lungs, the research team inoculated 8 ferrets with 10^5 pfu of CTan-H through trachea, and euthanized 2 animals on the 2nd, 4th, 8th and 14th days, respectively, and detected virus RNA in tissues and organs.
Among the two ferrets euthanized on the second day and the two ferrets euthanized on the fourth day, the researchers only detected viral RNA; in the turbinate and soft palate of one of them. Among the two ferrets euthanized on the eighth day, viral RNA; was detected in the soft palate of one ferret and in the turbinate, soft palate, tonsil and trachea of the other ferret. No viral RNA was detected in the two ferrets euthanized on the 14th day.
These results indicate that Covid-19 can replicate in the upper respiratory tract of ferrets for up to 8 days without causing serious illness or death.
At the end of the paper, the research team also mentioned that, comparatively speaking, Covid-19 is different from other influenza viruses that can replicate in the upper respiratory tract and lower respiratory tract of ferrets, and even human SARS-CoV. Covid-19 is only replicated in ferrets’ nasal bones, soft palate and tonsils. It can also replicate in the digestive tract, but even if the virus is inoculated in the trachea, the virus is still not detected in the lungs of ferrets.
Cats are highly susceptible to "cat-to-cat transmission": the monitoring of cat Covid-19 should be regarded as an auxiliary means of epidemic prevention and control.
It is worth noting that cats and dogs are in close contact with humans, so the research team thinks that besides laboratory animals like ferrets, it is very important to know the susceptibility of domestic animals that often live with humans to COVID-19 for the control of Covid-19.
The research team first studied the replication of Covid-19 in cats. Five 8-month-old subadult domestic cats (inbred lines) were intranasally inoculated with 10^5pfu of CTan-H, and two of them were scheduled to be euthanized on the sixth day to evaluate the virus replication in their organs. Three cats were put in separate cages in the isolator. In order to monitor the spread of respiratory droplets, an uninfected cat was placed in a cage adjacent to each cat vaccinated with the virus.
Because 8-month-old cats are aggressive, it is difficult to carry out routine nasal cleaning on them. In order to avoid possible harm, the research team collected the feces of these cats and checked the viral RNA in their organs after euthanasia.
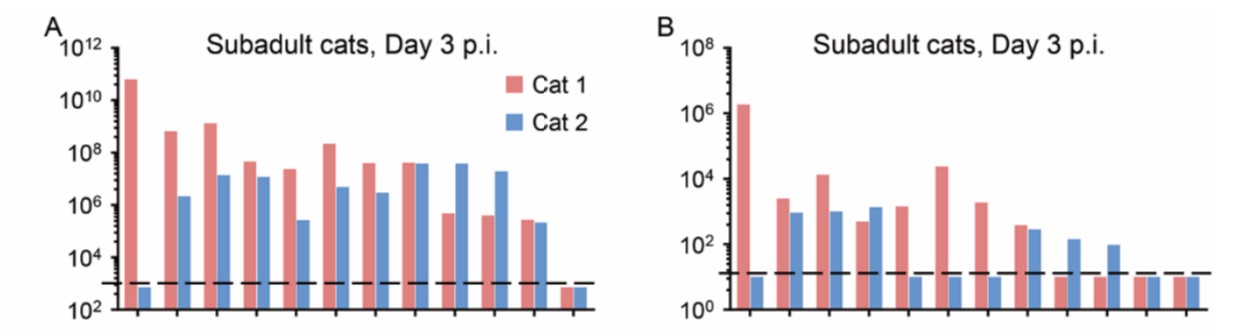
Virus RNA was detected in the nasal bone, soft palate and tonsils of two sub-adult domestic cats euthanized on the 6th day, and virus RNA was also detected in the trachea of one cat and the small intestine of the other cat. However, no viral RNA was detected in any lung samples of these two cats.
Infectious viruses were detected in the nasal bones, soft palate, tonsils and trachea of these cats, but no infectious viruses were found in the small intestine with positive viral RNA.

The spread of Covid-19 among cats.
In the study of virus transmission, RNA virus was detected in the feces of two vaccinated cats on the third day, and RNA virus was detected in the feces of all three vaccinated cats on the fifth day. Among the three cats at risk of virus exposure, viral RNA was detected in the feces of one cat on the third day.
Virus-infected cats with positive feces were euthanized on the 11th day. Virus RNA was detected in the soft palate and tonsils of the infected cats and in the nasal bones, soft palate, tonsils and trachea of the exposed cats, indicating that respiratory droplets spread between cats.
On the 12th day, the research team euthanized the remaining cats. Viral RNA was detected in the tonsils of one virus-infected cat and the nasal bone, soft palate, tonsils and trachea of another virus-infected cat, but it was not detected in any organ or tissue of the two virus-exposed cats.
Through ELISA and neutralization test, Covid-19 antibody was detected in all three cats inoculated with virus and one cat exposed to virus.

Covid-19 replicates efficiently in respiratory system and digestive system of infected cats, causing pathological damage and inflammatory reaction. Histopathological and immunohistochemical study on cats that died or were euthanized three days after virus infection. (a) The arrangement of nasal mucosa epithelium is disordered, cilia fall off (arrow), and lymphocytes in lamina propria infiltrate (arrow). (b) The tonsil epithelial cells are degenerated and necrotic, and the surface of mucosal epithelium (asterisk) is covered with cell fragments and neutrophils (arrow). (c) Epithelial degeneration and necrosis of tracheal mucosa (arrow), with mucus (asterisk) mixed with a large number of cell fragments on the surface. (d) Epithelial necrosis of tracheal mucous glands and infiltration of lymphocytes (arrow). (e) Normal lung tissue structure of uninfected cats. (f) Aggregation of inflammatory cells in pulmonary blood vessels and coagulation of fibrin (arrow). (g) A large number of macrophages and lymphocytes infiltrated in alveoli, that is, alveolar septa. (h) Infiltration and proliferation of alveoli and alveolar septitis. (i) Some cells in the epithelium of small intestine are degenerated and necrotic, and lymphocytes in the lamina propria are moderately infiltrated (arrow). (j) A large number of epithelial cells of turbinate mucosa were positive for virus antigen (brown). (k) A large number of exfoliated cells in tonsil mucosa epithelium and mucosa surface were positive for virus antigen (brown). (l) A large number of virus antigens were positive (brown) in serous cells of tracheal mucous glands. (m) A large number of small intestinal mucosal epithelial cells were positive for virus antigen (brown). Ruler line A, I = 100 μ m, B-H, J-L = 200 μ m, M = 500 μ m
The research team also repeated the above-mentioned replication and transmission research in sub-adult cats in young cats (70-100 days). Histopathological studies on the samples of young cats who died or were euthanized on the third day after being inoculated with the virus showed that the nasal cavity and tracheal mucosa epithelium and lungs of the two cats had a lot of damage.
These results indicate that Covid-19 can be effectively replicated in cats, and young cats are more susceptible to infection. More importantly, the virus can spread from cat to cat through respiratory droplets.

Next, the research team also studied the replication and spread of Covid-19 in dogs, and the results showed that dogs were less sensitive to Covid-19. Similar studies also show that pigs, chickens and ducks are not sensitive to Covid-19.
Overall, the research team found that ferrets and cats are highly sensitive to Covid-19, dogs are less sensitive, and domestic animals including pigs, chickens and ducks are not sensitive to the virus.
In addition, it is reported that Covid-19 uses angiotensin-converting enzyme 2 (ACE2) as its receptor to enter cells, and ACE2 is mainly expressed in type II lung cells and serous epithelial cells of ferrets’ tracheal-bronchial submucosal glands. Therefore, the research team believes that the potential mechanism to prevent Covid-19 from replicating in ferrets’ lower respiratory tract remains to be studied.
The results of this study show that ferrets can be used as animal models for vaccine and drug evaluation in Covid-19. Dogs, pigs, chickens and ducks are not susceptible to Covid-19, which has important guiding significance for the traceability of virus hosts; More importantly, cats are highly susceptible to Covid-19.
The research team called for close monitoring and protection of cats in epidemic areas to avoid contact with infectious sources and prevent them from becoming possible transmission hosts or storage hosts. The monitoring of cat COVID-19 should be regarded as an auxiliary means to eliminate the current Covid-19 epidemic.
Paper link: https://science.sciencemag.org/content/sci/early/2020/04/07/science.abb7015.full.pdf.